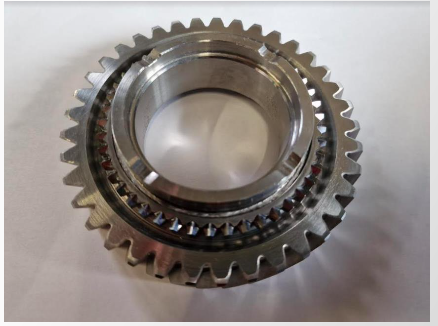
LASER WELDING ON AUTOMOTIVE GEARS
Nextema’s laser welding expertise enables crafting on automotive gears. Welds on these components are effective at high depths, presenting minimal distortion. In addition, the operation is easily repeatable, maintaining high quality and precision standards
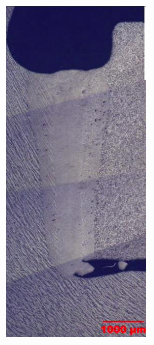
Automotive gear welding: is laser or electron-beam welding (EBW) better?
For welding automotive gears, laser welding is generally the preferred method
than electron-beam welding (EBW). Here’s why:
1. Speed and efficiency:
- Laser welding: it is faster and more efficient for mass production, which is a
great advantage in the automotive industry. It can be performed in air or with a
minimum protection, eliminating the need for vacuum, speeding up the process and reducing costs. - EBW: although it offers superior accuracy and deeper penetration, it is slower and
requires a vacuum chamber, making it less practical for high
productivity such as automotive production lines.
2. Accuracy and strength:
- Both laser and EBW welding provide strong, high-precision welds. However, for
gears, where a high degree of precision and minimal distortion are critical, the
laser welding is generally sufficient. - EBW would only be necessary if the gears were made of materials that require
very deep penetration or extremely tight tolerances, which is not usually the case
of typical automotive gear materials such as steel or alloys.
3. Heat altered zone and distortion:
- Laser welding: produces a small heat altered zone, which minimizes distortion-a
critical factor for gears, as they must maintain precise dimensions and tolerances to function
correctly. - EBW: also produces minimal distortion, but the additional precision provided by EBW is often
not necessary for automotive gears.
4. Conclusion:
Laser welding is more suitable for the production of automotive gears because of its speed,
lower costs, and the ability to meet the precision and strength requirements of automotive applications
automotive. Electron beam welding is a technology that is not optimized for this
application: it provides greater welding accuracy than is normally required, along with
higher costs and slower processing times.
Advantages of Laser Welding on gears
- High Accuracy: Laser welding allows enhanced accuracy levels due to the concentration of the laser beam, which proves to be especially useful on complex components such as gears.
- Reduced Thermical Distorsion: Heat is applied in a very precise and located manner, reducing thermical dsitorsion and deformation on gears. This is a critical feature in order to maintain the tight dimensional tolerances necessary for proper functioning of the welded gears
. - High strenght and durability: Joints created from laser welding tend to be more durable and strong, due to the precise melting of materials. This allows for a better durability of the gears.
- Process Speed: Laser welding can become a fast process, reducing production time and increasing efficiency.
- Automazione e Ripetibilità: La saldatura laser è facilmente integrabile in sistemi automatizzati, permettendo un’alta ripetibilità e qualità costante nei processi di produzione in serie.
- Rimozione del Materiale di Apporto: non è necessario utilizzare materiale di apporto, riducendo così i costi e semplificando il processo di saldatura.
- Flessibilità di Design: Permette una maggiore libertà nel design degli ingranaggi, poiché i limiti imposti dalle tecniche di giunzione tradizionali sono superati.
- Compatibilità con Materiali Diversi: La saldatura laser può essere utilizzata su una vasta gamma di materiali, inclusi acciai ad alta resistenza, leghe di alluminio e titanio, rendendola adatta a vari settori industriali.